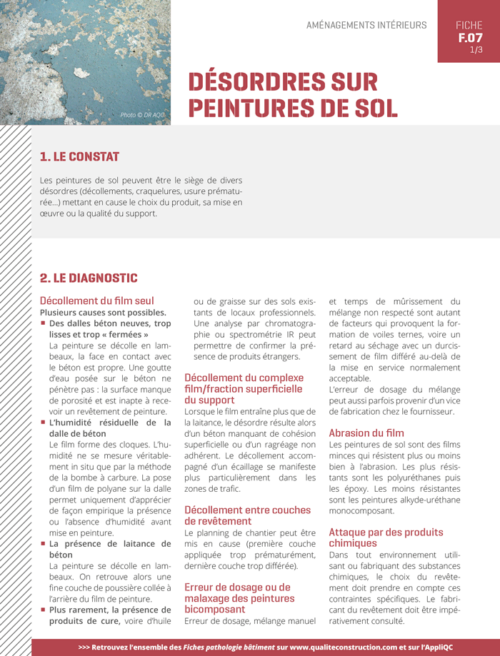
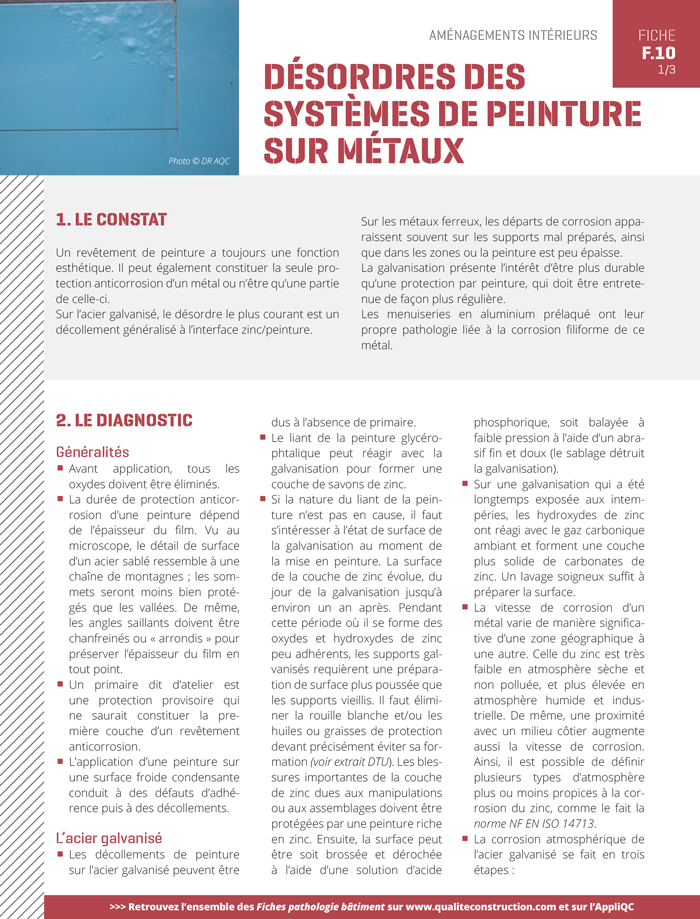
Désordres des systèmes de peinture sur métaux
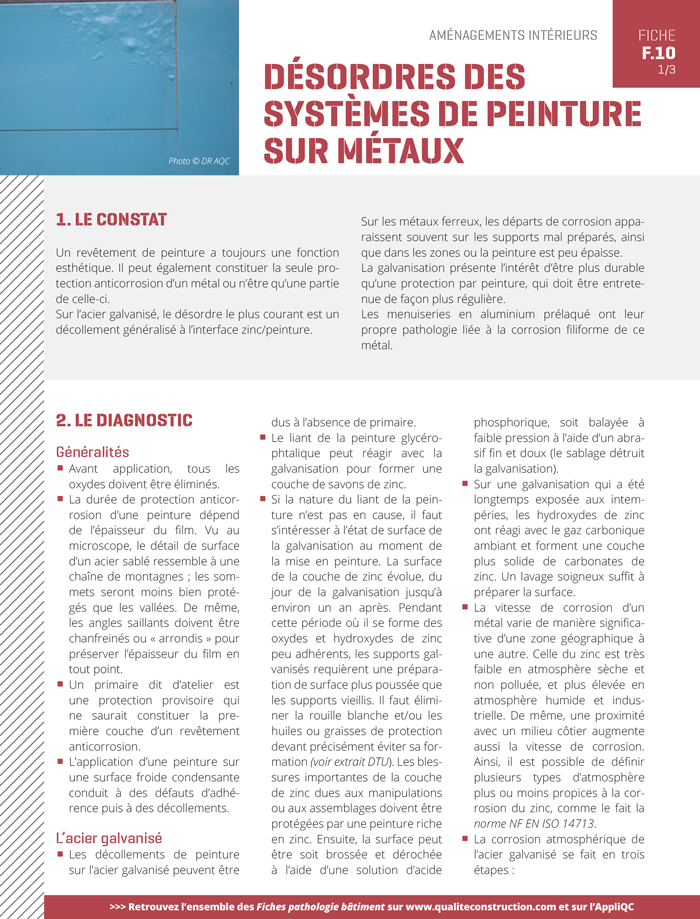
Collection : Fiches Pathologie bâtiment
Date de parution : 2024
Date de dernière mise à jour : Janvier 2024
SOMMAIRE
1. Le constat
Un revêtement de peinture a toujours une fonction esthétique. Il peut également constituer la seule protection anticorrosion d’un métal ou n’être qu’une partie de celle-ci.
Sur l’acier galvanisé, le désordre le plus courant est un décollement généralisé à l’interface zinc/peinture.
Sur les métaux ferreux, les départs de corrosion apparaissent souvent sur les supports mal préparés, ainsi que dans les zones ou la peinture est peu épaisse.
La galvanisation présente l’intérêt d’être plus durable qu’une protection par peinture, qui doit être entretenue de façon plus régulière.
Les menuiseries en aluminium prélaqué ont leur propre pathologie liée à la corrosion filiforme de ce métal.
2. Le diagnostic
Généralités
- Avant application, tous les oxydes doivent être éliminés.
- La durée de protection anticorrosion d’une peinture dépend de l’épaisseur du film. Vu au microscope, le détail de surface d’un acier sablé ressemble à une chaîne de montagnes ; les sommets seront moins bien protégés que les vallées. De même, les angles saillants doivent être chanfreinés ou « arrondis » pour préserver l’épaisseur du film en tout point.
- Un primaire dit d’atelier est une protection provisoire qui ne saurait constituer la première couche d’un revêtement anticorrosion.
- L’application d’une peinture sur une surface froide condensante conduit à des défauts d’adhérence puis à des décollements.
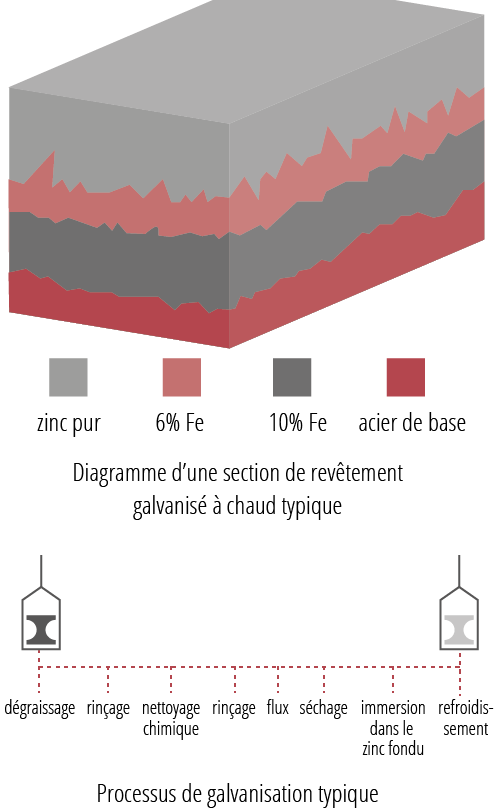
L’acier galvanisé
- Les décollements de peinture sur l’acier galvanisé peuvent être dus à l’absence de primaire.
- Le liant de la peinture glycéro-phtalique peut réagir avec la galvanisation pour former une couche de savons de zinc.
- Si la nature du liant de la peinture n’est pas en cause, il faut s’intéresser à l’état de surface de la galvanisation au moment de la mise en peinture. La surface de la couche de zinc évolue, du jour de la galvanisation jusqu’à environ un an après. Pendant cette période où il se forme des oxydes et hydroxydes de zinc peu adhérents, les supports galvanisés requièrent une préparation de surface plus poussée que les supports vieillis. Il faut éliminer la rouille blanche et/ou les huiles ou graisses de protection devant précisément éviter sa formation (voir extrait DTU). Les blessures importantes de la couche de zinc dues aux manipulations ou aux assemblages doivent être protégées par une peinture riche en zinc. Ensuite, la surface peut être soit brossée et dérochée à l’aide d’une solution d’acide phosphorique, soit balayée à faible pression à l’aide d’un abrasif fin et doux (le sablage détruit la galvanisation).
- Sur une galvanisation qui a été longtemps exposée aux intempéries, les hydroxydes de zinc ont réagi avec le gaz carbonique ambiant et forment une couche plus solide de carbonates de zinc. Un lavage soigneux suffit à préparer la surface.
- La vitesse de corrosion d’un métal varie de manière significative d’une zone géographique à une autre. Celle du zinc est très faible en atmosphère sèche et non polluée, et plus élevée en atmosphère humide et industrielle. De même, une proximité avec un milieu côtier augmente aussi la vitesse de corrosion. Ainsi, il est possible de définir plusieurs types d’atmosphère plus ou moins propices à la corrosion du zinc, comme le fait la norme NF EN ISO 14713.
- La corrosion atmosphérique de l’acier galvanisé se fait en trois étapes :
- une étape courte pendant laquelle une couche protectrice va se former : le carbonate de zinc
- une longue période où la couche de zinc se corrode
- et enfin, la corrosion de l’acier là où le zinc a été entièrement consommé.
L’aluminium
- Les profilés d’aluminium prélaqué exposés en milieu marin ou industriel peuvent être le siège de cloquages en forme de petites galeries en relief. L’analyse des éléments présents sous les cloques révèle la présence de chlorures qui en sont le facteur déclenchant.
- Les entreprises labellisées Qualicoat mettent en œuvre des gammes Qualimarine dont la préparation de surface plus poussée du métal apporte une meilleure résistance aux ambiances chlorées.
3. Les bonnes pratiques
- Réaliser une préparation de la surface du support bien spécifique à sa nature.Respecter les épaisseurs minimales des différentes couches, gage du bon résultat final.
- Respecter parfaitement les conditions limites d’application des produits : en température, humidité, ensoleillement, temps de séchage, et cela pour l’application et la phase de durcissement.
- Choisir la protection anticorrosion en fonction de l’agressivité du milieu et de la fréquence d’entretien souhaitée (pour l’acier, la protection la plus durable est une galvanisation à chaud, qui peut être recouverte de peinture pour des raisons esthétiques).
- Soigner la conception et le choix des produits : une bonne protection anticorrosion nécessite une conception soignée pour supprimer autant que possible les rétentions d’eau, accompagnée de préconisations détaillées des modes opératoires de préparation des supports, puis un choix de produits adaptés aux ambiances. Ces précautions seront encore plus importantes si les phases de reprises sont nombreuses avec des intervenants multiples aux différents interfaces « métal/subjectiles/peinture de finition », entre la fabrication, le montage, et la finition de l’ouvrage. L’examen des dossiers de sinistres fait souvent apparaître une cascade d’entreprises, à qui la commande finale a été passée sans aucune précision.
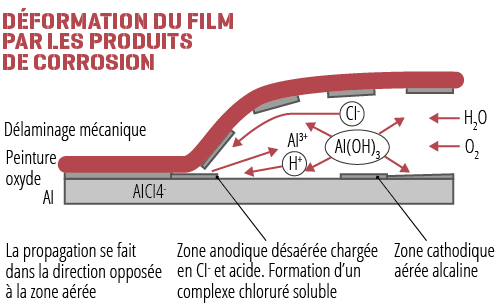
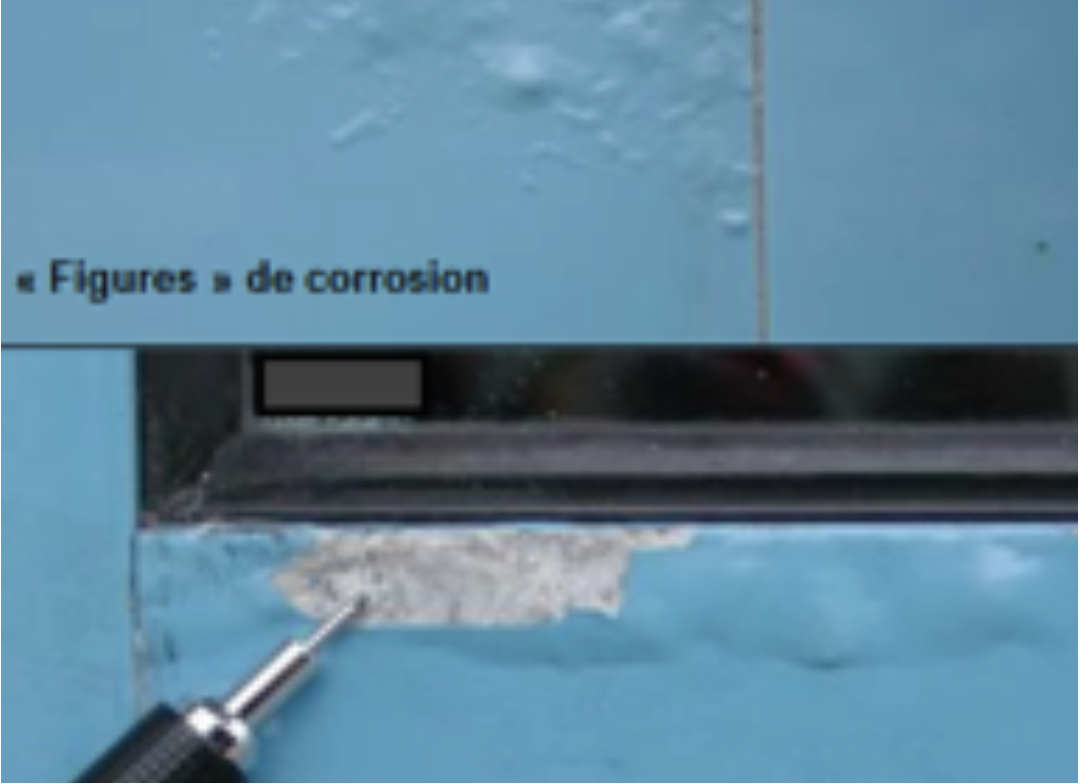
4. L’œil de l’expert
5. L’essentiel
- Soigner la préparation du support et l’exécution en respectant les conditions d’application des produits.
- Prendre en compte l’interface entre les entreprises intervenantes.
6. À consulter
- NF DTU 32.1 Travaux de bâtiment – Charpente en acier
- NF EN 1090-3 Exécutions des structures en acier et des structures en aluminium
- NF EN-1062-1 Peintures et vernis
- NF EN ISO 14713-1, 2 et 3 Revêtements de zinc
- FD T30-807 Peintures et vernis – Peinture pour le bâtiment
- EN ISO 4618 Peintures et vernis – Termes et définitions
- NF T36-005 Peintures et vernis – Classification
- NF EN ISO 4624 Peintures et vernis – Essais de traction
